A pottery table is essential equipment for avid potters, designed for wedging, hand-building, and sculpting clay. This sturdy table typically features a durable, easy-to-clean surface.
Crafting pottery requires precision, creativity, and the right tools, and the pottery table serves as the foundation for any ceramicist, whether they’re a hobbyist or a professional. It typically includes features like storage for tools and clay, as well as a comfortable working height.
Selecting the right pottery table involves considering size, material, and additional features such as adjustable height or portability. A quality pottery table can greatly enhance the efficiency and comfort of the pottery-making process, making it a crucial investment for anyone serious about engaging in this art form. With the right table, potters can streamline their workflow and focus on the creative aspects of their craft.
Choosing The Right Pottery Clay
Crafting a masterpiece at the pottery table starts with selecting the perfect canvas: the clay. This decision sets the stage for the form, function, and beauty of your creations. The right clay can transform an ordinary piece into a work of art, while the wrong one can lead to cracks, warps, or a finished product that doesn’t meet expectations. Understanding the nuances of clay is essential to ensure each project is not only aesthetically pleasing but structurally sound. Let’s dive into the specifics of pottery clay selection.
Types Of Pottery Clay
Embarking on a pottery project requires a keen understanding of the different types of clay available. Each type offers unique characteristics suitable for various techniques and finishes.
- Earthenware Clay – Known for its rich, red color and porous nature after firing; ideal for decorative pieces and hand-building techniques.
- Stoneware Clay – Versatile and durable, with a denser body; perfect for both hand-crafted and wheel-thrown pieces.
- Porcelain Clay – Highly refined, offering a smooth texture and a white, translucent finish when fired at high temperatures.
Considerations For Choosing The Right Clay
Consideration | Details |
---|---|
Firing Temperature | Match the clay’s firing range with your kiln’s capabilities. |
Forming Method | Ensure compatibility with wheel-throwing, sculpting, or hand-building. |
Final Use | Consider if the piece needs to be food-safe, waterproof, or purely decorative. |
Personal preferences in texture, elasticity, and the level of detail required also influence the choice of clay. Always contemplate the demands of the specific project before settling on a clay type.
Importance Of Clay Quality For Pottery Creation
The quality of the pottery clay cannot be overstated; it’s the foundation upon which all else is built. When the clay is of high quality, it behaves predictably through the forming, drying, and firing stages, reducing the chance of unsightly surprises. High-quality clay ensures the longevity and durability of the final piece, so it not only looks striking on display but can also withstand everyday use.
To ensure success, artists should opt for commercially prepared clay from reputable suppliers. This ensures consistency in the composition of the clay and peace of mind for the artist, allowing them to focus on the creative process rather than troubleshooting materials issues.
Essential Pottery Tools And Equipment
Embarking on the ancient and therapeutic craft of pottery requires adept skills, a creative touch, and, crucially, the right set of tools and equipment. Whether you’re a seasoned potter or just starting, understanding and having access to essential pottery tools can greatly enhance your craftsmanship. From the inception of a piece to its final firing, let’s delve into the indispensable tools that ensure functionality and finesse in pottery making.
Wheel Or Hand-building Tools
Choosing the correct tools for shaping and molding is vital, given that pottery can take form through either wheel-throwing or hand-building techniques. Below is a list of critical tools for both methods:
- Potter’s Wheel: A staple in wheel-throwing for creating symmetrical pieces.
- Rib Tools: Both wooden and metal ribs help in shaping and smoothing clay surfaces.
- Wire Cutters: Used to cut large chunks of clay and remove finished pieces from the wheel.
- Slip Trailers: Allow for precise slip decoration.
- Needle Tools: Essential for trimming and adding fine details.
- Modeling Tools: Different shapes and sizes are necessary for hand-building techniques.
- Slab Rollers: Flatten clay to an even thickness.
- Texture Mats: Impart unique designs onto the clay surface.
- Cutting Wires and Knives: Slice and define clay slabs.
Kiln And Firing Tools
The firing process demands precision and care. Ensuring the safe and correct firing of your pieces involves using the right kiln tools:
- Kilns: The critical chamber for firing pottery, available in a variety of sizes and fuel types.
- Kiln Shelves: Durable surfaces on which pottery is placed for firing.
- Posts and Stilts: Support pieces during firing and help maximize kiln space.
- Pyrometric Cones: Measure the heatwork inside the kiln to gauge firing completeness.
- Protective Gear: High-temperature gloves and safety glasses for handling hot pottery and kiln furniture.
Importance Of Quality Tools For Pottery Making
High-quality tools are the backbone of successful pottery. They provide the precision and control necessary for crafting exquisite pieces and, with proper maintenance, they can last a lifetime. Working with substandard tools can lead to frustration and inferior results. Investing in superior equipment allows for a smoother creative process, ensuring each piece reflects the potter’s intention and skill. From clay preparation to sculpting, glazing, and firing, quality tools help potters bring their vision to life with consistency and reliability.
Designing The Perfect Pottery Workspace
Embarking on the artistic journey of creating pottery begins with setting up a space that inspires creativity and allows for efficiency. Designing the perfect pottery workspace is about blending functionality with personal style, ensuring the environment is conducive to the flow of artistic expression. Whether you’re a seasoned potter or just beginning, the right workspace setup can significantly impact your craft.
Organizing the Pottery TableOrganizing The Pottery Table
An organized pottery table streamlines the crafting process and heightens productivity. Here’s how you can arrange your pottery haven:
- Tool Storage: Dedicated compartments or hanging systems ensure that tools are within reach but not in the way.
- Clay Management: Designate areas for fresh and recycled clay to avoid cross-contamination.
- Glazing Gear: Store glazes and brushes in an ordered fashion, potentially using labeled shelves or bins.
Lighting And Ventilation Considerations
Proper lighting and ventilation are crucial in a pottery studio. They not only affect the visibility and quality of your work but also your health. Take note of these insights:
- Natural Light: Large windows or skylights increase visibility and wellbeing. Supplement natural light with adjustable studio lamps.
- Air Quality: Pottery materials can produce dust; an air filtration system and adequate ventilation help maintain a clean and safe environment.
Ergonomic Setup For Comfortable And Efficient Pottery Making
An ergonomic pottery setup reduces the strain on your body and allows for prolonged creative sessions. Focus on these elements for a comfortable workspace:
Workspace Component | Consideration |
---|---|
Potter’s Wheel | Adjust the height to avoid hunching. A foot pedal within easy reach facilitates better control. |
Workbench | Ought to be sturdy and at an appropriate height to prevent back pain. Ensure it allows for free movement. |
Seating | Opt for a chair or stool that supports good posture. Comfort and mobility are key. |
Understanding Glazes And Finishes
A craftsman’s touch transforms simple clay into a piece of art, a transformation that owes much to the world of glazes and finishes. This crucial step in pottery not only provides a protective coating but also adds depth, vibrance, and personality to the final product. To appreciate the craftsmanship behind a pottery masterpiece, one must delve into the complexities of glazes and the subtle art of finishing.
Types of Pottery FinishesTypes Of Pottery Finishes
Various finishes can be applied to pottery, each providing a distinct look and feel. The primary finishes include:
- Gloss Finish: Reflects light vividly and adds a shiny appearance.
- Satin Finish: Offers a moderately glossy surface that strikes a balance between matte and gloss.
- Matte Finish: Gives a non-reflective, subtle and sophisticated touch.
- Crystalline Finish: Features distinctive crystal patterns on the glazed surface for an ornate look.
- Raku Finish: Known for its unique crackled texture and dramatic metallic effects.
How To Choose The Right Glaze
Selecting the perfect glaze involves more than personal style; it requires an understanding of the interaction between glaze and clay body, firing temperature, and the intended purpose of the pottery piece. Consider these factors:
- Matching Clay and Glaze: Ensure compatibility to prevent issues like crazing or peeling.
- Firing Range: Choose glazes that mature at the same kiln temperatures as your clay.
- Functionality: For items like dinnerware, look for food-safe, durable glazes.
- Aesthetics: Visualize the final look considering opacity, texture, and color.
Importance Of Proper Glazing Techniques For A Masterpiece
Without mastery in glazing techniques, even the best pottery can fall short of perfection. Precise glazing affects not only the piece’s durability and safety but also its artistic impact. Master potters exercise great care in:
- Application: Evenly distributing glaze to avoid runs or bare spots.
- Thickness: Monitoring to prevent cracking or bubbling.
- Firing: Carefully controlling kiln temperatures and atmospheres.
These steps ensure that final finishes highlight the potter’s skills and communicate their artistic intention effectively.
Maintenance And Care Of Pottery Tools And Workspace
Crafting pottery is an art that dates back thousands of years, yet remains deeply entwined with contemporary craftsmanship. Central to consistent success in this timeless practice are the maintenance and care of your tools and workspace. A well-maintained studio not only facilitates the creative flow but also ensures the longevity and performance of your tools and equipment.
Cleaning And Storage Of Pottery Tools
Proper cleaning of your pottery tools is fundamental in preventing clay buildup and corrosion. After each use, cleanse your tools with water, making sure to remove all traces of clay. Tools like rib tools, trimming tools, and wire cutters require special attention due to their sharp edges and intricate designs. Once clean, drying them thoroughly prevents rust from forming. Using a rust inhibitor on metal tools can further protect them from deterioration.
Regarding storage, organizing your tools in dedicated containers or toolboxes can protect them from the damage of a cluttered environment. Consider hanging larger tools on the wall or pegboard to save space and keep them within easy reach. Implementing silica gel packets in storage containers can help in controlling moisture, thus preventing rust.
Regular Maintenance Of The Pottery Workspace
A spotless workspace is essential for any potter. Regularly sweep floors and wipe down surfaces to maintain a dust-free environment. A clean studio is not only crucial for your health; it also prevents contaminants from spoiling your clay and glazes. Ensure that your pottery wheel and workbench remain in pristine condition by cleaning them after each session, checking for clay remnants or any signs of wear and tear.
- Inspect electrical equipment for signs of damage.
- Replace any faulty or worn components promptly.
- Achieve optimal lighting to avoid eye strain and to ensure the finest details are never missed.
Ensuring Longevity And Efficiency Of Pottery Essentials
To guarantee the longevity and efficiency of your pottery essentials, conduct a regular check-up of your pottery wheel’s moving parts. Lubricate according to manufacturer’s instructions to ensure smooth operation. For hand tools, consider applying a light coat of oil to maintain their condition.
Kilns—the heart of your pottery practice—require vigilant attention. Maintain a clear record of firing schedules and inspect for any cracked bricks or defective elements which might affect performance. Utilize kiln wash to protect shelves, ensuring an even heat distribution.
Tool Type | Maintenance Task |
---|---|
Hand Tools | Clean, dry, occasionally oil |
Pottery Wheel | Clean, lubricate moving parts |
Kiln | Inspect, clean, schedule repairs |
By observing these practices, you ensure the effectiveness and endurance of your pottery essentials, helping your tools serve you for many more creative projects to come.
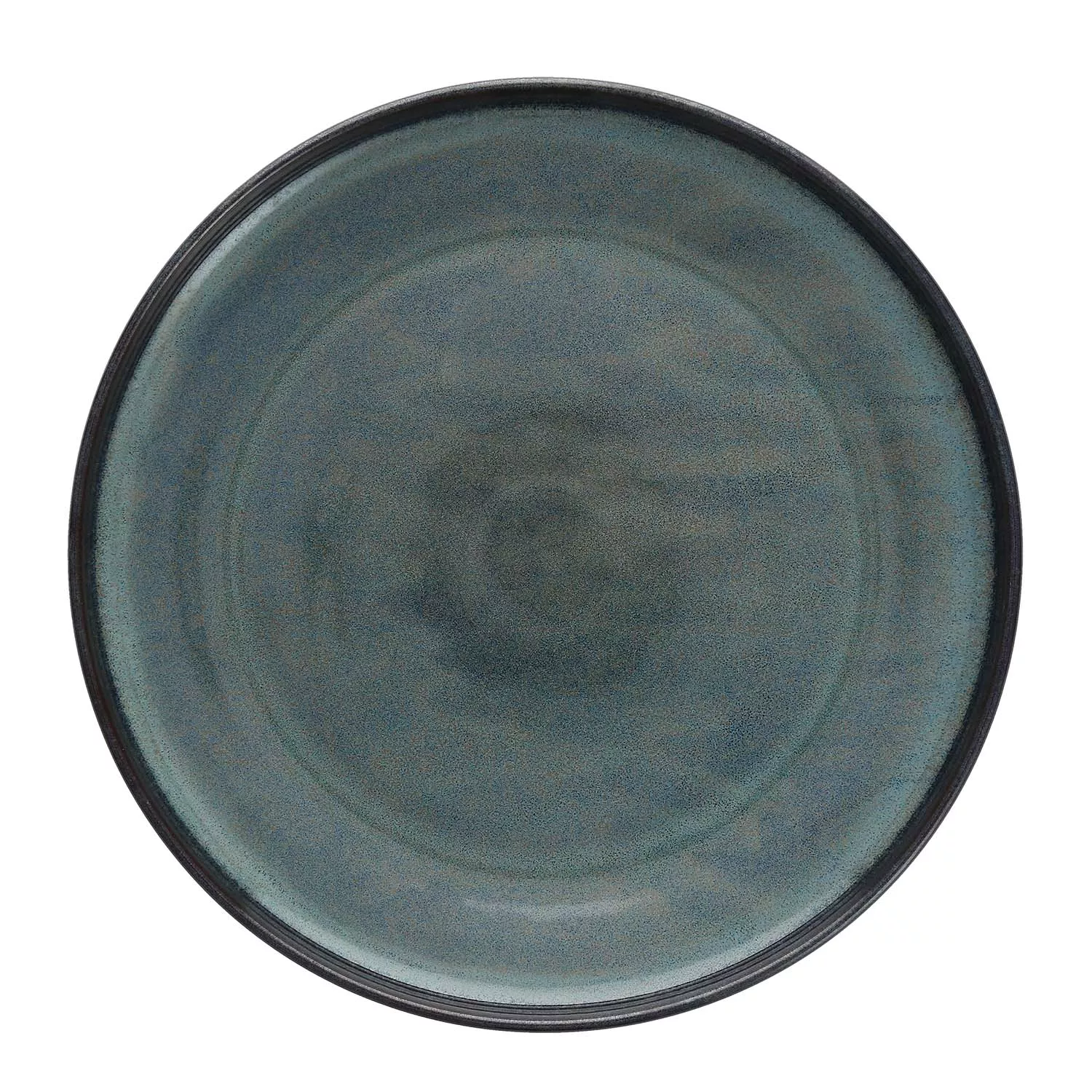
Credit: www.surlatable.com
Conclusion
Embracing the art of pottery can transform your space effortlessly. Let your creativity flow and infuse warmth into your home with a beautiful pottery table. Remember, each curve and glaze tells a story. Start shaping your own narrative today. Crafting memories, one piece at a time.